AOE3054 - Appendix 2 - Further information for Experiment 3
Appendix 2 - FURTHER INFORMATION FOR EXPERIMENT #3
Last Modified 23 January 2025
1. The open-jet wind tunnel
1.1 Construction details
Construction details of the open-jet wind tunnel are located at the following URL http://www.aoe.vt.edu/research/facilities/openjet.html.
1.2 Flow through the test section
Flow speed through the wind tunnel test section may be varied from zero to about
27 m/s. The flow quality in the test section has not yet been fully documented.
You are encouraged to try to produce such measurement (see Goal 5 in Section 4 of Experiment 3).
The
wind tunnel motor RPM is set remotely by a DC power supply (as shown in Figure 1) which at the same time is controlled by a MATLAB GUI described below. Variation
between the fan RPM and nominal freestream velocity is documented in Figure 2. This plot is used to estimate a required RPM to achieved
a desired freestream velocity. However, since a fan performance varies with atmospheric
conditions, a true freestream velocity must be measured with the pressure
system in the test section.
1.3 Associated equipment
The freestream velocity is calculated from the pressure acquired inside a
settling chamber of the wind tunnel. The settling chamber pressure (where velocity
is close to zero) is close to the stagnation pressure (p0) of
the flow in the test section, and therefore can be calibrated by applying Bernoulli's equation between the settling chamber and the room, and using the known contraction ratio of 5.5:1 (see 0.7m Open Jet Wind Tunnel website). Flow speed in the test section can also be monitored directly
using a 3-mm diameter Pitot-static probe (Figure 3). To get
the freestream velocity with the probe, you will need to ensure it is placed towards the upstream end
of the test section and away from the cylinder and edges of the jet where it is assumed to be unaffected by the presence of a
model. Note that placing a large model in the test section may artificially
increase the velocity sensed by the probe. All pressure systems are connected
to the Esterline pressure scanner for data recording and described below.
Further information on the Pitot-static probes is available in
Section
2
.
Temperature in the vicinity of the tunnel test section is monitored by a DS18B20 1-wire digital thermometer probe fixed to the side of the upstream frame of the test section (Figure 4). The probe is connected to Raspberry Pi, single-board computer which acquired the temperature in centigrade to an accuracy of ±0.5 degrees. Ambient (atmospheric) pressure is measured by a sensor in the Raspberry Pi Sense Hat (Figure 4). The sensor has a range of 260-1260 millibar with an accuracy of ±0.1 millibar. You can check the sensor reading and compare to results obtained from the airport data (determined from the altimeter pressure provided by the Blacksburg airport weather station):
All digital readings from the Raspberry Pi board are acquired through the data acquisition computer using a pre-designed Matlab GUI as will be explained in details further on in the user manual below.
A 3-axis traverse is located on top of the test-section mounting structure. Motion is achieved through a custom Velmex VMS linear slide system. The resolution of the programmable traverse is 0.25mm. The traverse coordinate system is set so that the positive X direction is pointing toward downstream, the Y direction is along the cylinder span and positive going away from operators, and the Z positive is pointing toward the floor (Figure 5). The drives will be preset for (X, Y, Z) = (0, 0, 0) at the midspan on of the cylinder axis and 140 mm downstream of the rearmost point of the cylindrical model in the X direction.
An Esterline pressure scanner 9816/98RK capable of measuring up to 48 pressures simultaneously is available for use with the open jet wind tunnel. The scanner is set so that each channel measures the differential between the pressure being sensed and the atmospheric. Channels 1-36 on the scanner are sensing the pressures from ports 1-36 on the cylinder. Channel 47 measures the static pressure inside the settling chamber. Channels 42 and 43 measure the static and stagnation pressures from the traversing Pitot-static probe. A picture of the pressure scanner can be found in Figure 2. The pressure scanner is an Ethernet based system that is connected to a computer using a RJ-45 cable (ethernet cable) and controlled using a Matlab program. A description of the code and all the instrumentation can be found in the user manual below :
A Pitot-static probe is perhaps the simplest device for measuring flow-velocity at a point.
A Pitot probe measures stagnation pressure (the pressure produced by bring the flow to a halt). It consists of a tube connected at one end to a pressure sensing device (such as a manometer or pressure transducer) and open at the other. Stagnation pressure is measured by pointing the open end of the tube towards the oncoming flow.
A static probe measures static pressure (the actual pressure in the flow). It consists of an opening (or 'pressure tap') parallel to the local flow direction. The pressure tap may be located in a tube (as shown in Figure 3), or in the surface of a model.
A Pitot-static probe is a combination of a Pitot tube and static tube. According to Bernoulli's equation the difference between the stagnation po and static pressure p is the dynamic pressure,
Given the flow density a Pitot-static probe can thus be used to measure velocity.
The principle sources of error in velocity measurements made with a Pitot-static probe are misalignment and turbulence.
Since the local direction of the flow around a model is not know in advance it is usual to make measurements are made with the Pitot-static probe pointing in the direction of the oncoming free stream. Some misalignment of the Pitot-static probe may therefore occur. Figure 7 shows typical errors in velocity measurements as a function of angle of misalignment. Errors become substantial for angles greater than about 30o.
A Pitot-static probe is designed only to measure velocities in a steady flow. In a turbulent flow, where the magnitude and direction of the velocity fluctuates with time, the Pitot-static probe measures, approximately, the time-averaged flow velocity. The errors in this measurement depend on the scale of the turbulent eddies encountered by the probe. If the open end of the probe is large in comparison to the turbulent eddies then the eddies stagnate and the end of the probe, artificially increasing the pressure difference it senses. If it is small then turbulent fluctuations in flow direction, produced as the eddies pass the probe, appear as misalignment and artificially decrease the measured pressure difference.

Figure 1. The open-jet wind tunnel default experimental setup.

Figure 2. Relationship between the wind tunnel fan and nominal freestream velocity at the test section.

Figure 3. Pitot-Static probe for velocity measurements.

Figure 4. Temperature sensor next to the test section entrance and Raspberry Pi Sense HAT for ambient pressure measurement.

Figure 5. Moving directions of the 3-axis traverse system
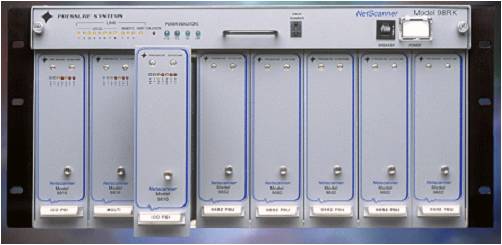
Figure 6. Esterline 9816/98RK Pressure Scanner
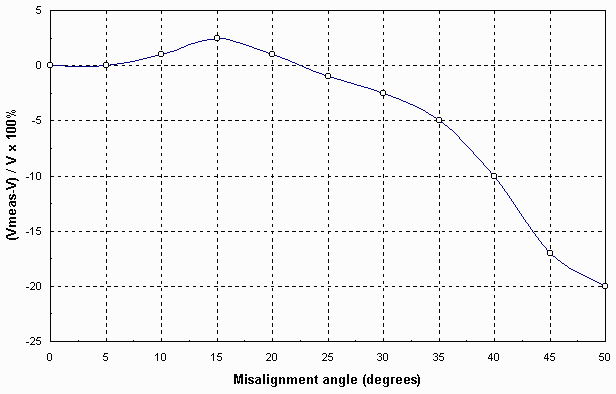
Figure 7. Errors due to misalignment in velocity measurements made with a Pitot-static probe. V - actual velocity; Vmeas - velocity sensed by Pitot-static probe; θ - angle of misalignment.