AOE3054 - Appendix 3 - Further Information into Experiment 7
Appendix 3 - FURTHER INFORMATION FOR EXPERIMENT #7
Last modified, February 2005
Overview
- This lab course primarily emphasizes the scientific foundations and basic tools required to conduct and analyze engineering tests. This appendix describes the procedures used in these tests. Engineering testing and simulation plays an extremely important role in aerospace engineering. Any engineering system must be tested before production is started. In aerospace engineering the systems are frequently developed through testing. In many cases this is called "simulation." Simulations use both computational and physical tests to evaluate and refine all aspects of an aerospace system. Many engineers are employed in both industry and government in this work, and high quality, high productivity testing and simulation is crucial to national competitiveness in aerospace engineering. This appendix provides an introduction to aerodynamic testing procedures. These procedures should be followed when planning any test, and should be used as a basis for conducting the wind tunnel tests in this course. This material should also be useful after graduation.
- Wind tunnel testing was used by the Wright brothers to develop their first gliders and the first controllable aircraft. As such, aerodynamic testing has a long history of contributing to the development of flight vehicles. During this time the procedures have become well defined. Nonetheless, conducting a successful test requires significantly more sophistication than might at first be expected. To obtain high quality data the test typically requires close coordination between a number of groups. This section provides a brief introduction to the procedures and steps associated with wind tunnel testing. Aerodynamic testing also involves flight test, flight simulators, and more unusual testing such as hover rigs for VTOL testing, and sometimes water tunnel tests. In recent years many aero test engineers have become test engineers in observables departments. Automobile companies are heavily involved in wind tunnel testing, with about half the effort devoted to external aerodynamics and half of the effort devoted to internal flow associated with ensuring adequate air flow for cooling.
- The book by Rae and Pope (Ref. 1) is an excellent introduction to aerodynamic testing, and should be used as a primary reference. Aerodynamic testing is not a pure science, and apprenticeship is the standard means of learning the methods. Many of the best documents are developed primarily for internal group training. Examples available from the author include references 2-6. This material is equally important to students who will not be directly involved in testing. Every aerospace engineer is at least indirectly involved in testing. Testing, and the high cost of testing, plays a key role in aerospace systems program schedules and development cost.
-
Traditional reasons to test range from physics oriented investigations
of basic fluid mechanics to measurements used in establishing design loads
for use in structural design of new, or modified, aircraft. Configuration
development is one of the key reasons to test. Despite the progress in
computational aerodynamics, aircraft configuration development is still
heavily dependent on wind tunnel testing. Development of the aerodynamics
math model used in creating flight control systems and evaluating aircraft
and flight control systems in manned simulation studies requires extensive
testing to define the aerodynamic characteristics throughout the flight
regime (
= -90° to + 90° at a minimum, over a large range of sideslip angles,
). Aerodynamic loads definition and math model development require a large amount of data after the configuration is completely defined and the configuration development job has been completed.
- Testing is conducted to develop testing methodology itself, develop component technologies, e.g. wing or inlet concepts among many, and aircraft development and modification. An emerging area of testing is associated with acquiring experimental data to validate computational fluid dynamics methodology.
- Test engineers are required to be familiar with the available wind tunnel facilities to determine what facility is best suited for a particular test requirement. There are a limited number of test facilities available for some of the more important types of testing. In addition to aircraft company facilities, the major large wind tunnels required to develop advanced vehicle systems are located at a relatively small number of locations in the US. In particular, the number of large transonic wind tunnels is very small and requests for test time must be made years in advance. Aero test engineers travel frequently, often spending weeks and months at the test site. Major wind tunnel facilities are located at:
- NASA Langley, Hampton, Virginia
- NASA Ames, Mountain View, California
- NASA Lewis, Cleveland, Ohio
- Calspan, Buffalo, New York
- AEDC, Tullahoma, Tennessee
- In many of these facilities the huge amount of electrical power required to move the air around the test circuit dictates that testing be done at night. At NASA Langley testing is reduced in the summer when the temperature is high and power must be used to satisfy residential and commercial air conditioning demands. When this happens the aero test engineer must literally "cool his heels" until the temperature goes down. Subsonic testing can be conducted at numerous locations in addition to those listed above. The "standard" subsonic wind tunnel test section is 7ft by 10ft., and many models are sized to fit that size wind tunnel.
- A remarkable variety of characteristics require testing. A partial list (each of which is also evaluated in flight test) originating with Meyer (Ref 6) is given here. This list is in addition to the basic configuration development testing, which might also include detailed flow diagnostics such as flow visualization. Each test objective will have a unique set of difficulties that must be taken into account to obtain high quality data for that specific item.
- Zero-lift drag
- Thrust minus drag
- Drag due to lift
- Drag rise (transonic drag divergence)
- Pressure distributions
- CLmax
- Stall characteristics (stability and control)
- Configuration sensitivity (Gaps-Overlaps)
- Dynamic effects
- Ground Effects
- Thrust Vectoring
- Basic longitudinal and lateral/directional derivatives, control effectiveness
- Conventional flight regime
- High angle of attack & stall data (static data) (famous Re effects on pitching moment)
- Dynamic data, .i.e. Spin Tunnel, free flight tunnel, and forced oscillation data
- Hinge moments (The first data mechanical controls guys want in design, not well estimated even in the tunnel tests.)
- Buffet onset, growth
- Wing rock
- Pressure distributions
- Component loads
- Wing
- Tail
- Fuselage
- Critical Flight Conditions (these are always a long way from design conditions)
- Aeroelastics
- Flutter
- Thrust minus drag
- Inlet stability - bleed requirements
- Power effects
- Acoustic, thermal environment
- Inlet distortion
- Boattail drag
- Figure 1 provides a case history of testing required to develop a modern aircraft, the F-16, and is based on data contained in the excellent paper by Hancock (Ref. 7). That paper also describes the important role that computers play in experimental aerodynamics. The breakdown shows the relatively small amount of testing devoted to the basic configuration concept, compared to the large amount required to define the characteristics after the configuration is defined.
-
The F-16 was developed in the early 70's. Today, the high angle of attack
characteristics would be more fully evaluated, with additional testing
compared to the F-16. This is in part due to the experiences with the F-16.
The angle of attack range where large regions of separated flow occur,
yet prior to the angle at which the flow is entirely separated (25°
<
< 50° for a typical modern fighter), is a critical flight region. In this region wind tunnel results are found to be sensitive to Reynolds number, support interference and possibly other effects. Results from different wind tunnels often produce different pitching moment characteristics. This is one area still requiring engineering judgment to interpret the results obtained in the wind tunnel.
- One area requiring extensive wind tunnel testing, but not covered in this course, is propulsion system testing. The airframe manufacturer is responsible for integrating the inlet into the configuration such that the engine is supplied with a uniform flow of air at the compressor face with minimal pressure losses. This is required for all flight conditions, and frequently leads to variable geometry in the inlet/diffuser system. The nozzle must also be developed. Traditionally, the engine manufacturer designs the nozzle. However airframe-propulsion integration requires that the components be tested extensively together.
- Most new engineers are involved in testing on large programs. More experienced engineers get involved in tests of new concepts and other specialized investigations. Because of the large amount of testing associated with aerospace design, the following material adapted from McLaughlin (Ref. 2) is included to help students gain an overview of the types of testing that occurs at various stages of aircraft system development.
- The types of aerodynamic testing conducted during aircraft development programs are:
- project task
- determine requirements
- investigate/screen technologies
- develop key technologies
- screen configuration possibilities
- screen weapons carriage possibilities
- screen propulsion system candidates
- aerodynamic wind tunnel test work
- component technology development
- airfoil study
- high lift system development
- control surface concept investigation
- powered lift concepts
- high angle of attack alternatives
- nose strake
- strakes
- auxiliary control surfaces
- propulsive control
- determine parametric effects of configuration integration
- component flutter tests
- isolated inlet tests
- project task
- requirements specified
- select propulsion system
- optimize & refine configuration
- define cost & schedule to develop
- aerodynamic wind tunnel test work
- gross refinement of configuration architecture
- performance verification
- proof of concept
- weapons carriage parametrics
- project task
- investigate alternate approaches
- perform cost effectiveness studies
- refine configuration design
- identify critical design issues
- aerodynamic wind tunnel test work
- detailed refinement of configuration architecture
- stability and control definition
- support simulation activity
- study spin & spin recovery characteristics
- performance verification
- preliminary loads definition
- preliminary weapons carriage definition
- project task
- resolve critical design issues (technology verification)
- refine configuration design
- start detailed design (long lead items)
- certify engine
- solidify data base
- aerodynamic wind tunnel test work
- technology certification
- level II aerodynamics loads definition
- update aerodynamic data base
- performance
- stability and control
- weapons carriage definition
- integrated inlet testing
- project task
- complete detailed design
- fabricate prototypes
- perform test & evaluation (ground and flight tests)
- begin pilot production
- aerodynamic wind tunnel test work
- periodically update aerodynamic data base in support of program milestones
- determine dynamic derivatives
- determine spin and recovery characteristics
- acquire weapons carriage & separation analysis data
- document performance & flying qualities of flight test article
- investigate safety of flight issues to support flight readiness reviews
- full configuration dynamic flutter tests
- The scale of the test activity, including planning, model fabrication, pretest, test and post test analysis is much more extensive than engineers unfamiliar with the process expect. Consider also that a similar effort is required for structures, flight control systems, propulsion systems, and every other component. This testing is required to ensure that the entire system performs safely and with the required performance. Unfortunately, the extensive testing required in modern aerospace programs is one of the key reasons for high development costs and long program development times.
- Pretest Planning
- Aerodynamic Test Planning: the objective and the scope of the test must be precisely determined before beginning to spend money on the test. Planning is important, a typical aerodynamic test program requires 6 mo. to 1 year minimum, and the cost can range from several hundred thousand to several million dollars. A complete full scale development (now EMD) test program will cover a six year period. The basic information required to determine the scope of the test and obtain the initial cost estimate is:
- budget restraints
- model availability
- test facility choice
- date of entry
- occupancy time
- speed regime
- model size
- test objective(s)
- model complexity
- Close coordination with all the participants is mandatory. With wind tunnel testing being so expensive, a well defined test plan with precise objectives has the best chance of resisting budget cuts. A major problem is justifying the need for as many tests as experience indicates are necessary during Engineering and Manufacturing Development (EMD). To solve this problem each test should be associated with a program milestone or anticipated documentation requirement.
- Division of Responsibility
- Normally the project requiring the test does not run the test directly. Within the organization a test group usually runs the test. When the test is going to be at another facility, you will also be interacting closely with their engineering staff. The following lists illustrate the typical division of work, and is based on the procedures used by a major airframe manufacturer.
- Aerodynamics Responsibility
- establish test requirement with project agreement
- establish funding & funding limitations (program authorization)
- designate a single point of contact for test coordination
- provide configuration details
- provide model aerodynamic loads information
- prioritize test objectives
- define required test conditions
- formulate run schedule overview
- approve most efficient run schedule proposed by aero test
- document pretest estimates of test results
- observe direction of the test, work with aero test engineer
- evaluate test results during the test
- analyze and document test results
- Aero Test Engineer Responsibility
- designate a single point of contact for test coordination
- provide cost estimates & monitor expenditures
- establish model design, fabrication, and test schedules and monitor progress.
- design model
- select appropriate test facility
- interface with test facility
- propose most efficient run schedule to meet test objectives
- provide pretest report to aerodynamics/facility/test sponsor
- monitor model fabrication, instrumentation installation and calibration
- conduct or supervise test at maximum efficiency (minimum cost)
- evaluate test data for measurement uncertainty and accuracy
- supervise data reduction and transmittal to aerodynamics
- provide post test report
- Note that both the aerodynamicist representing the project and the aero test engineer conducting the test must work closely together. With differing responsibilities, opportunities for conflicts to arise between the aerodynamicist and test engineer frequently present themselves.
- Model Design
- Successful test programs begin with a well designed model. The model should allow for easy change of parts, and provide for a means of precisely aligning the model in the tunnel. The model should be easy to work with in the tunnel. Attention to detail during the design will payoff during the test. Most subsonic models are made of wood built on an aluminum frame. Most high speed models are metal. If the model is large enough, aluminum can be used. If the model is small, steel may be required to obtain the necessary strength while maintaining the design contour. Model design and fabrication is a specialized field, and in addition to the major airframe manufacturers and government laboratories several smaller companies specialize in making wind tunnel models. These include Micro Craft, based in Tullahoma, Tennessee, and DEI (Dynamic Engineering, Inc.) based in Newport News, Virginia. Because of the specialized nature of the work, these companies can sometimes make a model faster and more cheaply than in-house machine shops.
- The most important consideration during fabrication is geometric accuracy. Unexpected errors frequently arise during fabrication. Before the days when surface shaded computer graphics were available the first view of the model occurred when the numerically controlled (NC) milling machine tape checkout piece was made. The aerodynamicist would frequently have an unpleasant surprise when examining this piece. Complex three-dimensional surfaces are difficult to visualize, and graphics should be used to verify the shape before releasing the lines to the NC tape programmers. Once the model is finished, it should be carefully inspected using a coordinate measuring machine over nearly flat surfaces, and templates cast normal to the leading edge and blown up 20 times on a comparator machine to document the actual model geometry. Model tolerances are usually specified in both absolute values and relative accuracy in terms of waviness. Tolerances should be tight around the leading edge, and are usually relaxed after the first 5-10% of the chord. It is unrealistic to specify a tolerance of less than .001 inches on a complex surface. Even this accuracy will require a highly skilled craftsman. Accuracies quoted by machine shops are frequently based on combinations of flat and exactly round surfaces. Accurately machined wing contours are more difficult.
- The Run Schedule
- The run schedule is a key item in structuring the test. It is used to establish the entry time requirement, and sequence of model changes. A run schedule is a list of the "runs" to made during the test. A "run" is usually a fixed configuration with data taken over a range of angles of attack (or side slip). Each angle of attack where data is taken is called a "point." A schedule is initially created as a "wish list," or straw man, and then, after the initial time and cost are estimated, scrutinized again by the facility and the originator. Wind tunnel time is frequently made available for a specific calendar time, based on the initial run schedule. Typically, the aerodynamicist doesn't get enough time to perform the complete set of runs identified on the run schedule. The run schedule is negotiated with the facility operators to define the tunnel occupancy time, and should be "massaged" by test engineers and the facility engineers to produce the most efficient use of facility capabilities within the time available. Recall that wind tunnel resources are limited, and there are great demands on national facilities from a variety of programs. The schedule is reworked to reflect changes in priorities as the test approaches.
- Once the test begins, the schedule will be altered based on the analysis of initial results obtained, and schedule problems. Model installation almost never goes as smoothly as expected, and normally no additional tunnel occupancy time is made available to make up for the lost time. In addition, initial results often mandate special unplanned runs to examine unexpected results. The ability to maintain a productive test program which maximizes the amount of data while reacting to surprises (problems) discovered in the data is a challenge that requires both concentration and talent. Engineers that can do this well are frequently called "tunnel rats." One well known tunnel rat is Irv Waaland, who was the project aerodynamicist on the Gulfstream II and F-14 programs at Grumman, and worked on the F-18 and B-2 programs at Northrop. Waaland won the AIAA Aircraft Design award in 1989.
- The following list provides some run schedule rules from another "tunnel rat," Charlie McLaughlin:
- Always begin with the simplest configuration (this is particularly true of a new model).
- Begin with a repeat configuration if the model or design was tested previously.
- Model parts availability & variability must be consistent with the run schedule.
- Make one model change at a time during configuration build up or modification activity.
- Make sure the resulting data comparisons are complete.
- Assign a priority to each run.
- When in doubt - make the run!
- Once the model is removed from the tunnel it may never go back in. An engineer's worst nightmare is to be assembling the test results for presentation to management and discover that a key run needed to make an engineering decision was not made. This could be a multi-million dollar mistake. The engineer running the test must make sure this doesn't happen. The best way to avoid this is to work with the data on site as it's available and, in effect, create your presentation to management during the test. You should be able to get off the airplane from the test site and go directly into the vice-president's office with your results in essentially final form.
-
Examples of several run schedules are shown in the figures. Figure
2 is from a Calspan test of the Grumman forward swept wing configuration
before it became the X-29. This is the actual test run log. The primary
information is the configuration description, a code describing the configuration,
the control settings, the angle of attack and sideslip schedules (as noted
above: a "run" usually consists of a single
or
sweep, with data being acquired at discrete "points") the Reynolds number, Mach number, and very importantly, a remarks column. The remarks column helps explain the purpose of the test, and any special problems. The remarks column does not replace the test notebook kept by the test engineer. The remarks column is the place to identify changes in the transition strip (these will be discussed below). In this case several Mach numbers were run for each configuration, and the run number is shown under the Mach number heading. The nomenclature requires additional explanation. Figure 3 shows a typical nomenclature sheet. Pictures of each nomenclature item should also be taken.
- Figure 4 shows a portion of a run schedule from a test at AEDC. In this case the run numbers are listed on the left hand side. This is more typical of subsonic run schedules similar to the schedule required for testing in the aerodynamics lab class. All the "codes" refer to the description of the configuration for use in the computer when performing data reduction.
- Special considerations in developing run schedules are required to obtain the reference conditions for use in data reduction. This includes initial runs to document the weight of the model in a particular configuration as it moves on the support with no wind load. These are called weight tare runs. This must be done for each different configuration which affects the distribution of weight. The forces and moments obtained during these runs are then subtracted from the wind-on results to find the aerodynamic forces on the model. Another set of early runs is frequently performed to subtract the internal flow drag, if a flow through inlet is included in the model. This drag is found using a pressure tube rake positioned at the exit of the nozzle. The internal drag of the duct is not part of the external aerodynamic force, and is properly included in an adjustment to the propulsion force.
- In most cases runs should be made early to determine flow angularity effects, and possible support interference effects. This would include testing the model in the upright and inverted position and through use of a dummy support system. Details are given in the reference by Rae and Pope (Ref. 1).
- Defining data requirements
- Accuracy requirements must be established early in the test planning process. They have a major impact on model design. The instrumentation and method of model fabrication will be determined by the accuracy specified. Over-specifying the accuracy drives the cost up, while poor accuracy could lead to results that are not precise enough to use, thus wasting the entire effort. Engineering judgment must be used to determine the necessary accuracy.
- The typical instrumentation compliment on an aerodynamic test would consist of:
- 6 component strain gage main balance
- surface pressure taps
- data correction measurements (determined by test engineer)
- model attitude measurements
- surface deflection angle measurement
- Additional instrumentation necessary for a component design/integration experiment (wing, tail, canard, store installation, propulsion system integration, other)
- auxiliary strain gage balances
- concentration of surface pressure taps
- flow survey rakes
- dynamic instrumentation to sense separation/buffet
- When running a dedicated loads test many strain gages and pressure taps are required.
- Additional instrumentation is required for a wing design investigation (at a minimum):
- 6 wing spanwise pressure tap stations (up to 150 pressure taps)
- wing root 3 component strain gage balance
- normal force, bending moment, torsion
- wing tip accelerometer to determine buffet onset determination
- flow visualization: oil flows, surface tufts, sublimation
- Other flow evaluation methods may be required. These include:
- hot wire anemometers, laser doppler velocimeter
- hot film gages (surface measurements), dynamic surface pressure measurements
- survey rakes, vortex probe, boundary layer survey probes
- sensitive microphones
- flow direction probes
- Flow visualization techniques
- Frequently the aerodynamicist needs to understand the flowfield in more detail than is apparent from overall forces, surface pressure distributions, and local balances such as root bending moment gages. Flow visualization is perhaps the most useful tool that an aerodynamicist has available to understand the details of the flow. The term "flow diagnostic" is usually employed to describe these types of tests. This testing is slow and currently produces primarily qualitative results. Therefore, in aircraft projects it's not done unless other results indicate that a problem exists requiring this information. Flow visualization is heavily used in research oriented testing.
- Flow visualization is generally divided into two types: surface and off-surface. For traditional, primarily attached flow aerodynamics, surface flow visualization is generally adequate. The types of information of interest include the transition location, separation location and shock position. Tufts are often used, and provide gross characteristics of the flow direction, separation lines, and indications of flow unsteadiness. Black silk thread attached with flat Scotch Magic tape, with the model painted light gray, works well. Yarn is also used frequently, and should be about two 1 1/2 to 2 inches long. They should be taped to the model in spanwise rows, spaced far enough apart that they don't interfere with each other. Four or five rows would work well on a six inch chord model. Figure 5 shows a typical layout of tufts on thre upper surface of a wing. The layout is shown schematically in Fig. 5a, and a photo of a tufted model is presented in Fig. 5b. Small silk tufts may oscillate too fast to see with the naked eye, and high speed photography may be required. Minitufts (Ref 1) also work well under the right conditions. Current VHS type video camera results often lack the resolution provided by traditional photography, and may be marginally valuable in making a record of the flowfield using tufts. Surface oil flows of one sort or another are useful, but extremely messy. Applying the oil, making the run, and cleaning up is a slow process. This makes oil flow testing thus costly (it's not uncommon to being paying a dozen engineers and technicians on each shift. The solvents that work best are probably no longer acceptable in most workplaces (trichloroethylene). Colored artist's oils thinned slightly on a white surface, applied as dots, works well. Alternating the colors can help trace the origins of the local flow. Unfortunately, some of the most spectacular oil flow studies I have seen occurred on competitive configuration development jobs, and aren't available for illustration of the technique.
- Figure 6 provides a sample of an oil flow photograph taken with a Polaroid camera at the NASA Langley 4-foot Unitary Plan wind tunnel at M = 1.62. In this case the oil shows a crossflow shock wave outboard on the wing, and a rare "open separation" associated with flow moving behind the shock from inboard upstream, creating a zone that the flow immediately upstream of the shock cannot penetrate.
- One of the most remarkable aspects of flow visualization is how quickly the observer may forget the details. It is extremely important to make the most detailed possible sketches and notes at the time of the test. It is easy to loose confidence when your boss is arguing that you "couldn't have seen" what you say you saw. Surface oil flows are relatively easy to document. Tuft probe work is not. No flow visualization recording technique is equivalent to observing the flow visualization directly with your own eyes.
- Off surface flow visualization is valuable when trying to understand flows with organized vortices and wakes. Surface results only provide a limited, and usually confusing, glimpse of the physics of the flowfield in these cases. Today the laser light sheet is one of the easiest ways to visualize the flow. Prior to the laser light sheet, tuft grids were used to gain insight.
- boundary layer studies
- oil flow - transition, separation, shock location, flow direction
- surface tufts - separation, flow direction
- sublimation - transition
- vortex flows
- laser light sheet
- tuft screen
- smoke
- bubbles
- tuft wands
- vapor screen
- schlieren
- flowfield studies
- shadowgraph
- schlieren
- interferometry
- water tunnel
- boundary layer separation
- vortex flows
- Details of these methods can be found in Rae and Pope (Ref 1).
- Fixing boundary layer transition
- This is one of the standard issues that must be resolved. The first question an aerodynamicist unknown to a facility is asked when he arrives at the tunnel is "what to do about transition?" This is a "rites of initiation" question that you had better be prepared to answer. Normally, after a lot of discussion the facility engineers end up using "the usual procedure" for that tunnel. The location of transition from laminar to turbulent flow is controlled by putting surface roughness on the model.
- Why do you fix transition?
- so that the transition position is known
- so that the flight boundary layer characteristics are better simulated at critical conditions
- How?
- Carborundum grit
- glass beads
- serrated tape
- wires
- Where?
- at various locations on all model components
- Who determines?
- aerodynamics, aero test and the test facility - jointly
- There are basically two different considerations, leading to two different methods in defining transition. The simplest is the requirement that the model have a fully turbulent boundary layer, or at least a known state. This allows the aerodynamicist to make an adjustment to zero lift drag to estimate flight values from wind tunnel data with some confidence (see section 2 for further discussion). The second type of boundary layer transition is associated with proper modeling of the boundary layer at shocks and at the trailing edge. This is associated with modeling the boundary layer near separation, and is mainly associated with drag due to lift. This is usually the critical consideration at transonic speeds. The first method is usually used for subsonic and supersonic testing, while the second method is associated with transonic testing. An extremely precise procedure might reposition the transition location for each angle of attack. Clearly this is impractical for most testing, and engineering judgment must be used to decide the best approach to simulating full scale conditions.
- Fully subsonic and supersonic test conditions
- Braslow method (NASA TN-D-3579, Ref. 7)
- fix transition near the leading edge
- transition strip height and streamwise location a function of test Reynolds number and Mach number
- method is generally used at all test conditions to fix transition on all other model components
- at subsonic speeds trip strip height is generally within the boundary layer so that no drag correction for the strip is necessary
- at supersonic speeds it may be necessary to determine a grit drag correction experimentally by testing various strip heights
- Mixed flow (transonic conditions)
- Blackwell method (NASA TN-D-5003, Ref. 8)
- fix at a further aft wing location to better simulate the flight boundary layer at the wing shock location and/or the wing trailing edge
- transition strip height and location a function of test Reynolds number, Mach number and shock location
- computational viscous airfoil analysis used to determine location
- Braslow method used to determine height
- percent chord location can vary spanwise due to wing taper
- trip must be located at least 5% chord ahead of the shock to avoid laminar shock boundary layer interaction
- boundary layer must be kept laminar to the trip by keeping model surface smooth
- Special case - aft cambered wing lower surface
- fix further aft to provide a better flight boundary layer simulation in the region of adverse pressure gradient caused by aft camber
- avoids cove separation that could occur at lower test Reynolds number
- The exact details of the procedures are beyond the scope of these notes. The reader should consult Rae and Pope (Ref 1). However, the essential idea is that a roughness element is selected to give a roughness element length based Reynolds number of 600 at a streamwise location corresponding to a running length Reynolds number of 1.x106. This assumes that the flow at this point has not undergone premature transition due to adverse pressure gradients. This presents a problem for subsonic flow at high lift, where suction peaks are immediately followed by a rapid recompression very near the leading edge.
- In many standard aerodynamic configuration tests at subsonic speeds, black electrical tape cut by pinking shears is used. The tape is positioned about 5-10% aft of the leading edge. The pinked edge is placed facing into the flow. Sometimes, several layers are used.
- Pretest estimates
- The importance of pretest estimates cannot be overstated. Without pretest estimates it is impossible to know if you have a potential problem, or to be able to assess whether the objectives of the test are being achieved. The aerodynamicist must be able to determine at the test if the data fails to agree with pretest estimates because of a data reduction error, or if an actual aerodynamic problem exists on the model. This is similar to debugging a computer program. In either case immediate action must be taken, and adjustments to the run schedule may be required. Pretest estimates are frequently required to use government facilities. The government sponsor will attend the test and plot your experimental drag polar and predicted pressure distributions on the same sheet (or screen) with your pretest estimates. At this point your company will either establish credibility with the sponsor or begin a corrective action program to establish credibility (this could mean your job).
- To summarize - pretest estimates are crucial, they:
- provide an immediate indication of test procedure and/or data reduction problems
- provide an immediate indication of model design and/or fabrication problems
- provide an immediate indication of aerodynamic design problems
- estimates generally assume an optimum design
- the problem can be either due to the actual aerodynamic configuration or with the estimating methodology
- One classic example of test work based on pretest estimate discrepancies is the story of how the Grumman concept for the forward swept wing concept arose. The forward swept wing idea resulted from the transonic test of an aft swept wing of a Grumman configuration which had been proposed to satisfy the NASA HiMAT RFP (request for proposal). The winning proposal was submitted by Rockwell, and the Rockwell HiMAT was built, flown, and is currently in the Smithsonian Air and Space Museum.
- After Rockwell was selected, NASA still expressed interest in the Grumman wing design, and offered to test it. Initial results indicated that the pretest drag estimate was 20% optimistic compared to test results at the maneuver design point (MDP). The cause of the problem was traced to the empirical drag estimating methodology. It was too approximate for the class of advanced airfoil technology used in the wing. On-the-spot rethinking of the estimation method, using some additional runs at the test site, resulted in an improved method that resolved the discrepancy. Different wing sweep angles were studied. This was accomplished easily because the model had a variable sweep wing (other aerodynamicists have yawed models to study slight changes in sweep). The new drag estimation method (and understanding) provided the first clue that a forward swept wing might be optimum for the HiMat maneuvering design goal: 8 gs sustained at .90 Mach number and 30K feet altitude. Without precise expectations based on pretest estimates the forward swept wing idea would not have emerged. Glenn Spacht was the aerodynamicist who did the work in the tunnel at NASA Langley. This effort resulted in his advocacy of forward swept wing aircraft and his career advanced quickly. He was deputy project manager of the X-29 program and is now director of engineering at Grumman.
- In addition to precise estimates, more approximate estimates are required to locate and size the balance and determine ranges for pressure gages. Structural analysis will be based on these estimates. Model safety analysis will depend on them. A recent development is that some facilities (AEDC) will request the model geometry in a numerical format which allows them to make their own computational analysis to determine if the objectives of the proposed test can be achieved using the proposed approach.
- Test
- Many issues must be considered in conducting the test. Items that must be checked when preparing to run the test are discussed in this section.
- Tunnel flow calibration issues: The flow in a wind tunnel is not an exact simulation of flight in free air. The tunnel flowfield will vary in velocity and direction throughout the section. Some freestream turbulence will be present in the wind tunnel flow. Any tunnel will have a flowfield survey describing the quality of the basic flow. The quality of the flow will vary between wind tunnels. The Virginia Tech Stability Wind Tunnel has extremely good characteristics (see section 5). Sometimes the facility operators will not be particularly eager to show users the details of the flowfield, but will specify where the model should be positioned in the test section to obtain the best results.
- Force balance calibration: One of the most important considerations in testing is the accuracy of the balance. The balance should be check loaded every time a model is installed. These results should be available for use in the data reduction program.
- Model Support Interference: The model support system will produce a deviation from the flowfield that the actual airplane would encounter in flight. This interference is minimized by wind tunnel, model design, but is never eliminated, and must be considered during data reduction. To assess the magnitude of these effects several experimental techniques are used. Rae and Pope (Ref. 1) describe methods for correcting the test results to attempt to eliminate these effects from the data. This is a problem area where computational aerodynamics can be used to get insight into the way in which the support is interfering with the model.
- Fouling and removal of base/cavity drag: Several rather subtle aspects of testing can be troublesome. The first is known as fouling, and occurs when the support system hits the portion of the model supported by the balance. This arises because of the desire to make the smallest possible deviation of the model to accommodate the balance and the deformation of the model under load. This can be checked by installing a fouling circuit strip, such that if the model touches the support an electric circuit is completed and a warning is issued at the operators console. Temptation to save installation time and run without a fouling strip can lead to acquisition of questionable data and is a false economy. Frequently it is hard to determine if fouling exists without the fouling strip.
- Another important aspect of aerodynamic testing is the correction required to account for base or cavity drag that does not exist on the actual vehicle. This requires the measurement of a base or cavity pressure, and the determination of the area over which this pressure acts. Cavity pressures should be checked early during testing to make sure that the correction is being made properly.
- Axis issues: Care must be taken to ensure that the axis system is understood. If the balance is mounted on a strut the measurements will be made in a wind axis system nominally aligned with the tunnel. If the balance is located internally in the model the forces will be measured in a body fixed coordinate system. The usual axis systems are the wind, stability and body axis systems. Most aerodynamic performance analysis requires results in the stability axis (lift and drag). Stability and control work may be done using either axis. High angle of attack stability and control analysis is usually carried out in the body axis. It is generally easier to understand the effect of a conventionally oriented control device using the body axis because they are generally designed to produce a pure moment about a specific body oriented axis. Airframe manufactures may use either system, and this is sometimes a source of confusion when companies engage in joint ventures. Figure 7 from Ref. 5 illustrates the sign convention and relationship between axis systems.
-
Transformations from Rae and Pope (Ref. 1) are repeated
here. Note that the data should be translated to a common origin, and then
rotated using the angle of attack,
, and angle of yaw,
: For data analysis the sideslip angle
is usually taken to be -
. The subscript "sa" denotes stability, "w" denotes wind, and "B" denotes body based axis systems. In the body axis system lift and drag are replaced by normal and axial force, and are used without subscripts. Here c is the mean aerodynamic chord and b is the reference span.
- Stability axis results are obtained from the wind axis results through:
- CLsa = CLw
-
CDsa =
CDwcos
- CYwsin
-
Cmsa =
Cmwcos
+ (b/c)Clwsin
-
Clsa =
Clwcos
+ (c/b)Cmwsin
- Cnsa = Cnw
-
CYsa =
CYwcos
+ CDwsin
- Body axis results are obtained from wind axis results through:
-
CN = CLwcos
+ CDwcos
sin
+ CYwsin
sin
-
CA = CDwcos
cos
- CLwsin
- CYwsin
cos
-
CmB =
Cmwcos
- (b/c)Clwsin
-
ClB =
Clwcos
cos
+ (c/b)Cmwsin
cos
- Cnwsin
-
CnB =
Cnwcos
+ Clwcos
sin
+ (c/b)Cmwsin
sin
-
CYB =
CYwcos
+ CDwsin
- The wind axis coefficients can be obtained from the body axis coefficients using:
-
CLw = CNcos
- CAsin
-
CDw = CAcos
cos
- CNsin
cos
+ CYBsin
-
Cmw =
CmBcos
+ (b/c)ClBcos
sin
+ (b/c)CnBsin
sin
-
Clw =
ClBcos
cos
- (c/b)CmBsin
+ CnBsin
sin
-
Cnw =
CnBcos
- ClBsin
-
CYw = CAcos
sin
+ CYBcos
- CNsin
sin
- Numerous corrections to wind tunnel data may be required to predict the corresponding values that would occur under actual flight conditions. Figure 8 illustrates a few of the issues that must be considered. Several chapters of Rae and Pope (Ref 1) contain details. One fundamental data adjustment not shown is the weight tare, which is the balance reading with the model moved through the test range with the wind off. This must be subtracted from the wind off force to get the aerodynamic force. Usually a table is created and interpolated for the combinations of angle of attack and yaw used in the actual test. A table is required for each configuration with a different mass distribution.
- Flow angularity adjustments are required because the freestream velocity is not precisely aligned with the tunnel centerline. As shown in Fig. 8, when the balance is mounted on the strut, the measured readings must by transformed, and the angle of attack corrected using the following relations:
-
true =
meas +
up
-
CLtrue = cos
upCLmeas - sin
upCDmeas
-
CDtrue = sin
upCLmeas + cos
upCDmeas
-
Ideally the flow angularity,
up, is small. When this is the case, these equations show that the correction to the value of lift is small, but the correction to drag can be large. This is one of several reasons that drag is difficult to measure in a wind tunnel. The flow angularity is best found from a careful test using a reference wing in both the upright and inverted positions, with a dummy strut system. Alternately, the tunnel survey with no model present can be used. Sample survey results for the Virginia Tech Stability Tunnel are contained in section 5.
- Another correction is required to account for test boundary effects. These are different depending on the type of boundary; solid, open, or slotted. As long as the model is small compared to the test section the corrections should be small. Wind tunnel wall correction theory is not yet complete, and a variety of advanced wind tunnel concepts have been proposed to minimize them.
- Post Test Analysis
- Final data reduction/analysis: As described above, the data reduction program should be verified, and the initial data plotted together with the pretest estimates before leaving the test. In most facilities the only difference between the data available on site during the test and the final data is due to the use of more elaborate averaging process and the correction of problems identified during the test while comparing with the pretest analysis. The elaborate averaging process usually doesn't change the results by an amount that can be plotted on a normal report scale. Data reduction system errors are frequent, and will likely never be completely understood unless identified during the test. Without pretest predictions it is virtually impossible to spot these problems. Examples include the wrong sign on a tare correction (responsible for a major problem once when a full scale V/STOL model, including two operating TF-34 engines, was being tested in the NASA Ames 40x80 tunnel); incorrect removal of base drag at the sting cavity, and failure to take into account misalignment between the model axis and the sting axis. Sometimes a reference condition is incorrectly entered, and the balance is assumed to be broken when in fact the data is good. I have encountered all these problems at one time or another.
- Documentation/Final report preparation: The technical requirements are addressed in section 3, Presentation of Aerodynamic Data. In determining the final report contents, the test engineer will consult with the project and determine:
- types of curves desired (plotting schedules)
- selection of scales
- type of curve fits to be used in connecting data points
- comparison plots to be made
- Other analysis included in the post test report include plots providing Reynolds number effects, and transition strip effects, both transition strip on and off, but also strip size and location effects.
- Wind tunnel to flight data corrections/extrapolation: This effort is strictly speaking not part of the aerodynamic testing problem, but is closely associated to the application of wind tunnel data to actual aircraft predictions, and has a direct bearing on the planning and conduct of the test. It is discussed in some detail section 2.
- Safety is a key consideration in planning and conducting an aerodynamic test program. People die during test operations. Not often, but I'm personally aware of several cases. In one case the model technician was working under a large powered Grumman model lent to NASA Langley for their use. The sting support failed, and the technician died after being crushed by the model. For this reason, safety must be a key consideration during model design. A stress analysis, documented in a stress report, must be done for the model, and the model-balance-support system under all the loading conditions. A stress analysis must also be done for all appendages to the model. The facility will require these reports before model installation and testing can begin.
- Model scale wings and especially canards and tails are often extremely sharp, and engineers and technicians working around models are frequently cut. In some tunnels the model is hoisted above the tunnel and lowered into the test section using a ceiling crane. In one case I was, luckily, working the other shift at McDonnell when the workers hoisted the model too fast. It started swinging back and forth. One of the technicians tried to keep it from hitting the wall by jumping in the way to stop it. His whole shoulder was crushed.
- Occasionally an engineer stands inside the tunnel test section during tests to probe the flow with a tuft wand. Extreme care should be taken when this is done. Safety goggles must be worn. Finally, a video camera should be used to monitor the engineer (unlike the Virginia Tech Stability Tunnel, in many tunnels the operator cannot physically observe the test section), and a hand should be kept on the emergency stop button.
- Two other test procedures require special safety considerations. High pressure air is always potentially dangerous, and care must be taken working with it. The final item is associated with the introduction of lasers into aerodynamic testing on an almost routine basis. In particular, laser light sheet flow visualization is extremely valuable. However, in examining the flowfields in laboratory conditions it is sometimes very easy to be tempted to look directly into the sheet from the side. Special care should always be taken to avoid eye damage. Most facilities have established strict procedures for working with laser systems.
- Engineers are required to consider safety, and must be prepared for investigations resulting from tests they plan, design or conduct, when an accident occurs. NASA requires a stress analysis and an aeroelastic analysis as part of the pretest safety review before testing in their tunnels. They are concerned for both human safety and possible damage to the tunnel if the model fails. One joint Grumman/NASA Langley program resulted in a model/support system combination that was dynamically unstable at high angle of attack. During one test in the Langley Full Scale Tunnel the dynamics resulted in a sting system failure. The oscillation built up so fast that on the video of the test (always a good idea) you couldn't see the failure. One instant the model was in the picture, and the next instant it wasn't. Several incidents have occurred where a key major national facility was closed for a year or more after a failure during testing. Due to the control on model safety, in most cases the tunnel structure and not the model caused the accident. Flight operations are even more rigorous regarding safety.
- Once the test is conducted, adjustments are made to the results to apply them to the full scale vehicle at flight conditions. This is a step where judgment is required, and it is not unusual for the aerodynamicist to err at this stage. The consequence of a mistake here can be very serious, and aerodynamics managers frequently demand details and caution here.
- A somewhat standard list of corrections (assuming that the usual corrections to account for wind tunnel wall effects, etc. have already been made) to wind tunnel data include:
- Model scale effect:
- Skin friction (Reynolds number and transition location): This is frequently the most significant correction made to the data.
- CLMAX - this adjustment is crucial, and is difficult.
- Support system interference and modifications made to the model to accommodate the sting installation.
- Airplane protuberances and surface roughness not simulated on the model. Geometry and surface finish (includes all cooling inlets and vents, all antennas, etc.)
- Propulsion/internal flow related: Airplane secondary air systems not simulated, nozzle geometry not accurate (often arising from item 1), incompatible or inadequate inlet spillage drag conditions.
- Explicit power effects
- Aeroelastic effects - more difficult with respect to aeroelastically tailored shapes.
- Frequently theoretical and computational aerodynamics methods are used to estimate these effects. Otherwise, adjustments are made based on previous results obtained experimentally. Since each aircraft company has a different experience base, the adjustments will differ slightly among companies. For example, consider the problem of extrapolating the minimum drag obtained in a wind tunnel test to flight conditions. If the geometry is the same for your model and the full scale vehicle (which it usually isn't, as discussed below), then the primary consideration is the skin friction. Typically, a theoretical estimate is made of the skin friction at both the model and flight conditions. The difference between the theoretically estimated drag computed at the two different conditions is then added to the experimental results to estimate the minimum drag of the vehicle at full scale conditions. This is one of the reasons that it is critical to know how much laminar flow exists on the model. Otherwise, the model friction estimate may be very poor.
- Even with advances in computational and experimental techniques, several aspects of wind tunnel to flight adjustments still require further research. The following list presents some of the more notorious:
- Reynolds number sensitive data
- Supercritical airfoil and winglet test requirements
- "Scaling" buffet intensity data
- Sensitivity to model lines/accuracy
- Support interference/dynamics
- Controlled transition/grit selection
- Consistency of high alpha data
- Tunnel turbulence
- Tunnel wall interference
- Reflection plane models for drag
- There's no simple way to extrapolate from wind tunnel to flight operation of aircraft with total confidence. Reference 10 provides a basic primer on the subject. To get some insight into the wealth of complications and problems that arise, look at the important NASA work on the XB-70 (Ref. 11).
- You rarely have the same geometry in flight that you tested. It was 15 years before Grumman had a model of the F-14 that actually corresponded to the flight article. For the F-14, as with most configurations, the configuration was "tweaked" one last time after the last wind tunnel test. The only reason Grumman eventually did have an accurate F-14 was that the AMRAAM program needed one and they were willing to pay for a new model. Other typical situations include vortex generators added during flight test programs but not addressed in original drag estimates/tests, and the gap/step correspondence between wind tunnel models and flight hardware.
- There always seems to be a disagreement over exact performance of the engine. This makes accurate flight test drag values difficult to obtain. Many, many corrections are made to the engine data. Usually there's a lot of money at stake. Both the airframe and engine must meet performance guarantees, with large penalties if they aren't met.
- Another complication is the reliability of initial flight test results. The issue of flight test data accuracy further complicates the comparison between wind tunnel and flight test data. When the flight test data first arrives and the inevitable panic begins, experience shows that the flight test data system itself may be suspect, although the flight test group usually refuses to acknowledge the possibility. Two particular cases that I had some involvement with were the discrepancy between tunnel based estimates and flight test results for the loads on the vertical stabilizer of the EF-111 (upper transonic, M = 1.1, windup turns), and cruise drag of the Grumman-American Gulfstream III executive jet.
- In the first case the initial flight data was over predicting the discrepancy by about 100%, and about 50% was real. A redesign of the vertical tail structure of the EF-111 was required (recall that the EF-111 differs from the F-111 by the addition of a large electronic jamming antenna placed on the vertical tail-the EA-6B has a similar pod but never flew in this speed regime). During the ensuing "fire drill" the Air Force program office was demanding daily viewgraph presentations of the results of the Grumman investigation!
- In the second case the discrepancies were apparently traced to the use of a reflection plane model and two separate problems. Reflection plane models are notorious for poor drag results. The G-II reflection plane model tunnel to flight increments (which were found to agree nicely with flight data) were applied to the G-III reflection plane results. The first problem was that the G-III wing was added to the basic G-II reflection plane model, resulting in a wingspan that was too large for the tunnel. The second problem was that tunnel to flight increments for "conventional" (actually the British developed peaky) airfoils and the supercritical type airfoil used, at least in part, on the G-III scale differently between tunnel and flight (this involves the proper way to fix transition).
- Cases similar to the ones described above usually aren't documented in the literature; they're not stories the participants are particularly proud of. In the end, when working with the data you begin to get a feel that you understand the problem and can account for everything. i.e. that you have "the story" (but you can't prove it scientifically).
- Another famous (possibly the most famous) case involved the tunnel to flight pressure distribution on the C-141 wing. The shock in flight was much stronger and further aft than had been found in the wind tunnel. This led to trim changes and additional drag. At the time the difference was attributed to Reynolds number effects, and was used to convince congress that the a new wind tunnel was needed which could simulate flight Reynolds number using wind tunnel models (this requires that testing be carried out at very low temperatures using near liquid state nitrogen). This wind tunnel has now been built (after having been designed in large part by a VPI grad, Blair Gloss), is located at NASA Langley, and is known as the National Transonic Facility (NTF). Subsequently we tried to use this case to demonstrate the capability of computational methods to simulate Reynolds number effects. The results were disappointing, with only about half the shock movement predicted by our computational methods. When discussing our results with engineers familiar with the C-141 data, we were told that the Reynolds number was only part of the story, the other being wall interference effects. To achieve flight Reynolds number for at least marginally affordable costs the NTF is basically an 8 foot tunnel. Our biggest transonic wind tunnels are 16ft square. Thus the wall interference issue still exists in the NTF.
- To conclude: Using "raw" wind tunnel data and making simple skin friction adjustments to estimate flight data may easily result in a 10% difference between tunnel and flight. The critical areas in the flight regime are almost always more complicated than first appearances. However, once you work at understanding the full story, you generally feel that you can account for the differences within a few counts. Original drag estimates made at the time that a production decision was made may not take into account a lot of the effects that occurred after the estimates were made, or did not turn out in hindsight to be wise interpretations of data. Engineering judgment is still required, and experienced engineers will be required to make tunnel to flight correlations and analysis for the foreseeable future.
- The format established for the course should be used. The following comments are specific to aerodynamic testing, and may not be generally applicable.
- Text (two aspects of the test report are critical)
- 1) In the documentation of the test enough detail must be included from the test to settle any question that comes up after the test is over. This includes the test run schedule, configuration nomenclature description, sign convention for deflecting surfaces, and the so-called "tab data" from the test. The test engineer must keep a detailed notebook during the test, and include extreme detail in the test report. Many well annotated photos should be included. Many times questions arise (sometimes years later) where the documentation is insufficient to determine with certainty exactly what happened. Few of us can remember particular test details even after a few months, and particularly when being grilled because something doesn't "look right" (this is the situation as soon as the flight test data arrives, as described above). Two typical personal examples include exact details of transition fixing, and sign convention for deflection of surfaces (at high angle-of-attack it may not be at all obvious what effect a "plus" or "minus" deflection would produce on the aerodynamic results). Since a typical test might cost several million dollars, and the data might be examined for effects that weren't of specific interest during the test, good documentation is crucial. An unfortunate, but frequent, occurrence in practice is that the time and budget expire before the test report is completed. Since it's done last, budget overruns frequently result in poor final documentation. It's best if the report can be put together while the test is being conducted. This approach can minimize the problem.
- 2) In the data analysis portion of the report: When writing the report provide specifics, not generalities, i.e., rather than "greater than," say "12% greater than." What do the results mean? In large organizations the test engineer will write a test report precisely documenting the test, while the project aerodynamicist will write the report analyzing the data. When writing the analysis, do not simply provide tables of numbers and demand that the reader do the interpretation. The conclusion to be drawn from the each figure must be precisely stated.
- Plots and Graphs
- Use real graph paper. For A size plots this means K&E2 Cat. No. 46 1327 for 10x10 to the half inch, and an equivalent type for 10x10 to the centimeter. There is an equivalent catalog number for B size paper. Wind tunnel data (especially drag polars) are often plotted on B size paper. This is Albanene tracing paper. It's what's actually used in engineering work, and it's expensive. The University Bookstore stocks this graph paper. You should use it carefully, and not waste it. With high quality tracing paper, where the grid is readily visible on the back side, you plot on the back. This allows you to make erasures and also produces a better looking plot. Orange graph paper is standard, and generally works better with copy machines. The tracing paper also allows you to keep reference data on a set of plots and easily overlay other results for comparison. Remember to allow for overlay comparisons by using the same scale for your graphs.
- Always draw the axis well inside the border, leaving room for labels inside the border of the paper. Labels should be well inside the page margins. Data plots should contain at least:
- reference area, reference chord and span as appropriate (include units)
- moment reference center location
- Reynolds number, Mach number, and transition information
- configuration identification
- Use proper scales. Use of "Bastard Scales" is grounds for bad grades in class and much, much worse on the job. This means using the "1,2, or 5 rule". It simply says that the smallest division on the axis of the plot must be easily read. Major ticks should be separated by an increment that is an even multiple of 1, 2 or 5. For example, 10, 0.2, 50. and 0.001 are all good increments between major ticks because it makes interpolation between ticks easy. Increments of 40, 25, 0.125 and 60 are poor choices of increments, and don't obey the 1,2, or 5 rule. The Boeing Scale Selection Rules chart in included as figure 9. Label plots neatly and fully. Use good line work. In putting lines on the page, use straight edges and ship's curves to connect points, no freehand lines. Ship's curves and not French curves are used by aeronautical engineers, and some catalogs call them aeronautical engineering curves. The University Bookstore stocks at least the most common ship's curve size. As a young engineer, I was told that if the wind tunnel data didn't fit the ship's curve, the data was wrong. More often than not this has indeed turned out to be the case.
-
Drag polars are traditionally plotted with CD on the
abscissa or X-axis, and CL on the ordinate or Y-axis.
Moment curves are frequently included with the CL -
curve as shown in Figure 10. The moment axis is plotted from positive to negative, also shown in the figure. This allows the engineer to rotate the graph and examine Cm-Cl in a "normal" way to see the slope.
- More comments on proper plots and graphs are contained in your engineering graphics text, by Giesecke, et al. (Ref. 12). The engineer traditionally puts his initials and date in the lower right hand corner of the plot. An example of an acceptable plot is included as figure 10.
- Can you use your computer to make plots and graphs? Of course. But they must be of engineering quality. To achieve this you certainly have to understand the requirements given above for hand plots, and have made enough graphs by hand to be able to identify problems in the computer generated graphs. Often it's easier to make plots by hand than to figure out how to get your plotting package to do an adequate job. Typical problems include poor scale selection, poor quality printout, and inability to print the experimental data as symbols and the theory as lines. Another problem that arises is the use of color. While color is important, it presents a major problem if the report is going to be copied for distribution. Most engineering reports don't make routine use of color - yet. A final problem frequently arises with the labeling. In reports, the figure titles go on the bottom. On view graphs and slides the figure titles go on the top. Many graphics packages are oriented toward placing the figures on the top. This is unacceptable in engineering reports.
- Aerodynamic forces must be accurately measured. Initial aerodynamic testing used simple scales. Today most force measurements are made using strain gage balances. At large facilities the strain gage balances are designed, built and maintained by an instrumentation group that usually consists of mechanical engineers. However, you should understand the principles of operation. Balances must be selected for a particular test based on the physical size and loads demanded on the balance. Each balance should have a drawing indicating the size and on the same drawing you will usually find a table containing the maximum loads. Sizing and placement of the balance requires use of the pretest loads estimates made by the aerodynamics group. Typically the strain gage balance is located inside the model at a position near the aerodynamic center to minimize the possibility that the pitching moment limit will be exceeded. This can be a little challenging if the same model is to be used for both subsonic and supersonic testing, and in cases where component build-up testing may lead to situations where the pitching moment becomes large (also variable sweep wings). In some cases provision for two balances might have to be made.
- Frequently aerospace companies and government agencies borrow balances to obtain the correct size. Balances are delicate and can be easily damaged if handled improperly. Their installation in models requires precision machining, and therefore, the balance is pinned in place. The portion of the model that produces loads measured by the balance is known as the metric portion of the model. Accounting for the metric and non-metric parts of the model are sometimes tricky, especially in powered model testing, where the forces over portions of the model are desired. Powered model testing is one of the most challenging areas of aerodynamic testing. Frequently the propulsion group needs more wind tunnel test time than the aerodynamics group.
- Because the balance must reflect the loads accurately, care must be taken when "bridging" the balance. This means that a minimum of cables and pressure tubes should cross from the metric to the non-metric part of the installation. In some cases this means that a scanivalve or its equivalent should be placed inside the metric model to allow surface pressure and force and moment results to be acquired simultaneously. The scanivalve measures pressures from a number of orifices and allows many pressures to be transmitted to a single pressure transducer. Thus, rather than having 48 pressure tubes bridging the balance, the only lines that crosses the balance are the scanivalve, control cable, and possibly a reference pressure tube. Frequently this results in a severe temperature and vibration environment for this instrumentation, and possible problems should be considered during pretest planning.
- A strain-gage balance measures forces and moments by sensing deformation of a beam-like element that has a strain gage attached to it. The balance is based on the principle that the electrical resistance of a conductor changes when subjected to mechanical deformation. A strain gage is a small, thin printed circuit type electrical resistance element which changes its resistance when elongated or compressed (Fig. 11a). This gage, which may be on the order of 1/4 inch square or smaller, which is glued onto a structural element which will be affected by the force to be measured.
- A simple strain-gage balance to measure drag can be made using two strain gages on a single beam as shown in Fig. 11b. As a drag force is applied, the upstream gage element feels tension and the downstream element compression due to the bending in the beam. Since the signs of the resistance changes on the two elements are opposite, taking their difference by placing them in a circuit such that they subtract will result in a doubly strong resistance change. Any change due to a pure "upward" or "downward" force through the other beam will thus cancel out. This is important because temperature induced effects arising from thermal expansion of the material would result in misleading indications of an externally applied force.
- The change in resistance can be detected by either using a constant voltage supply and measuring a current change or by using a constant current and measuring the voltage change. The resulting reading can then be calibrated by comparing the output signal under a range of test loads. Unless the gage or beam is over-stressed, the readout will be a linear function of the force applied.
- Only one problem exists with the balance design in Fig. 11b, the gage output is really determined by the bending moment, which is a function of the distance between the application point of the force and the gage element location, as well as the force magnitude, instead of being a function of the force alone. A remedy to this is shown in Fig. 11c where 4 gage elements are used. Now, the circuitry can be set up to read two individual moments M1 and M2 due to the applied force and subtract them. The difference between these two moments is a function only of the force and the fixed distance between the two sets of gage elements. Since this distance is constant, the drag can be directly determined by a single circuit regardless of the location of the applied force on the beam. The circuitry for such an arrangement is shown in Fig. 11d where gage elements 1 and 2 are in tension and 3 and 4 are in compression.
- A wind tunnel strain-gage balance has at least one such "bridge" to measure each force and moment. For more information on strain gage balance design see Rae and Pope (Ref. 1).
- The full description of the Stability Wind Tunnel is located on the World Wide Web at the following URL https://www.aoe.vt.edu/research/facilities/stabilitytunnel.html.
- Rae, William H., Jr., and Pope, Alan, Low-Speed Wind Tunnel Testing, Wiley & Sons, New York, 1984.
- McLaughlin, C.B., "Experimental Aerodynamics and Configuration Design," Grumman Aerodynamics Lecture Series, May, 1985.
- Toscano, E.J. "Aero Test Notes - Basics of What a Wind Tunnel Test Engineer Should Know About Internal Strain Gage Balances, or What a Model Designer Must Know About Internal Strain Balances and Other Things," Grumman internal notes.
- Nark, T., "Powered Lift Testing," First Atlantic Aeronautical Conference, Williamsburg, Virginia, March 26-28, 1979. (Boeing Company Viewpoint)
- Hedrick, I.G., "Using Wind Tunnel Test Results," Lecture XII, Introduction to Aerospace Engineering, MIT, May 3, 1982.
- Meyer, R., "General Information on Wind Tunnel to Flight Correlation," Grumman Memo EG-ARDYN-80-150, December 15, 1980.
- Hancock, G.J., "Aerodynamics - the role of the computer," Aeronautical Journal, August/September, 1985, pp. 269-279.
- Braslow, A.L., Hicks, R.M., and Harris, R.V., Jr., "Use of Grit-Type Boundary-Layer-Transition Trips on Wind-Tunnel Models," NASA TN D-3579, Sept. 1966.
- Blackwell, J. A., Jr., "Experimental Testing at Transonic Speeds," in Transonic Aerodynamics, ed. by Nixon, D., AIAA Progress in Astronautics and Aeronautics, Vol. 81, AIAA, New York, 1982, pp. 189-238.
- E.J. Saltzman and T.G. Ayers, "Review of Flight to Wind Tunnel Drag Correlation," Journal of Aircraft, Vol. 19, No. 10, October 1982, pp 801-811.
- "Wind-Tunnel/Flight Correlation Study of a Large Flexible Supersonic Cruise Aircraft (XB-70-1)"
- Part I, NASA TP 1514, James C. Daugherty, Nov. 1979.
- Part II, NASA TP 1515, John B. Peterson, Jr., Mike Mann, Russell Sorrells, Wally Sawyer and Dennis Fuller, Feb. 1980
- Part III, NASA TP 1516, Henry Arnaiz, John B. Peterson, Jr. and James C. Daugherty, Mar. 1980
- Giesecke, F.E., Mitchell, A., Spencer, H.C., Hill, I.L., Loving, R.O., and Dygdon, J.T., Principles of Engineering Graphics, Macmillan Publishing Cop., 1990, pp. 591-613.
- Ahn, Seungki, Choi, Kwang-Yoon, and Simpson, Roger L., "The Design and Development of a Dynamic Plunge-Pitch-Roll Model Mount," AIAA Paper 89-0048, January, 1989.
1.1 Where you test, what you test
Aircraft Performance
High Lift
Stability and Control
Unsteady Aero
Aerodynamic Loads
Propulsion-Airframe
1.2 Testing related to aircraft
development
Conceptual Study Phase | |
---|---|
|
|
Concept Definition Phase | |
|
|
Preliminary Design (alternative systems exploration) | |
|
|
Demonstration/validation phase (pre-full scale development (FSD) phase) | |
|
|
Engineering and Manufacturing Development (EMD), Formerly known as Full Scale Development (FSD) | |
|
|
1.3 Aero test procedures (based
on Ref. 2)
The following list summarizes the available techniques:
2. Use of Wind Tunnel Data in Aerodynamics (based in part on Ref. 6)
Recognized Wind Tunnel Problem Areas
1 This appendix was reviewed at Grumman under the direction of Casper Catalanotto, Group Lab Manager, Aerodynamics Test, Ground Testing Technology, Grumman Aircraft. John McAfee and Howard Jarvis contributed. Revisions were made to incorporate their comments.
2 This paper is very high quality paper. With computers replace hand plotting, this paper is being discontinued by K&E. Most art supplies stores (sometimes erroneously claiming to be engineering supply stores also) don't stock good graph paper. Cheap paper will not be transparent, allowing easing tracing from one plot to another.
Figure 1 Example of the testing required to develop a modern fighter
aircraft (Ref. 7).
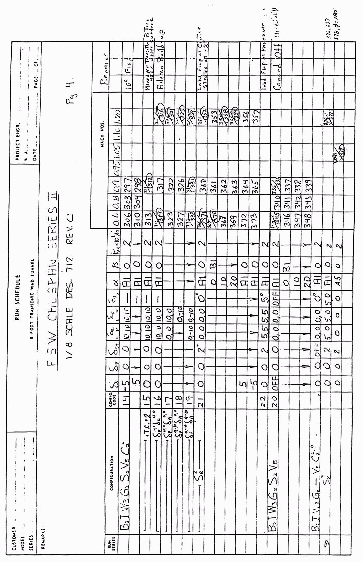
Figure 2. Typical run schedule: transonic, run numbers under Mach heading
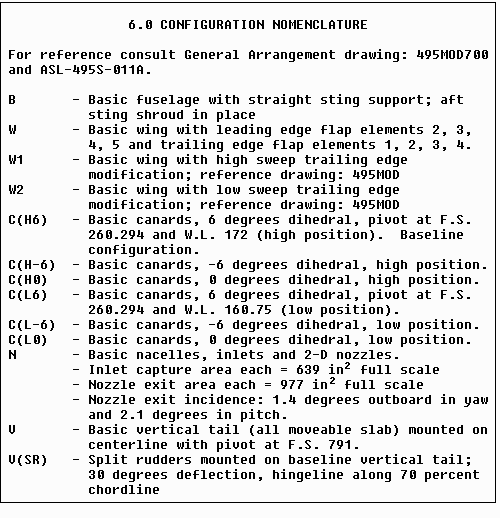
Figure 3. Typical nomenclature chart associated with run schedule.
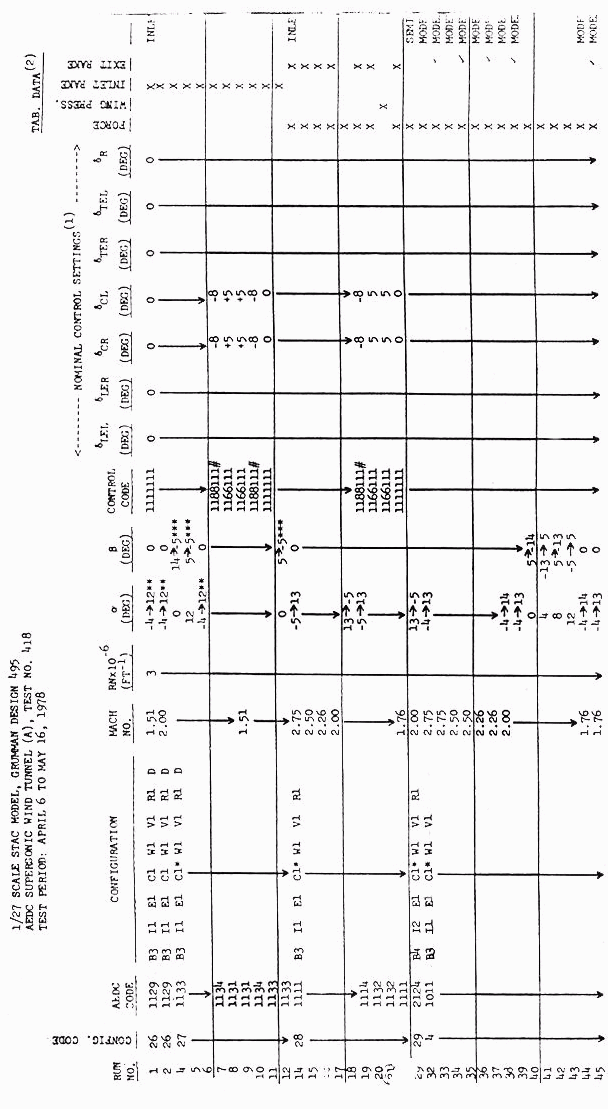
Figure 4. Typical run schedule with run numbers on the left hand side. Defining data requirements

a) Typical methods of attaching tufts. Only A is suitable for high speed work. (Ref. 1)
b) Typical tuft layout on the upper surface of a wing (Ref.
1)
Figure 5. Illustration of the use of tufts for flow
visualization. from Grumman Aero Report 393-81-1, October, 1981, "Experimental
Pressure Distributions and Aerodynamic Characteristics of Flat and Cambered
Conceptual Wing-Body and Wing-Body-Canard Models at M=1.62," by W.H. Mason.
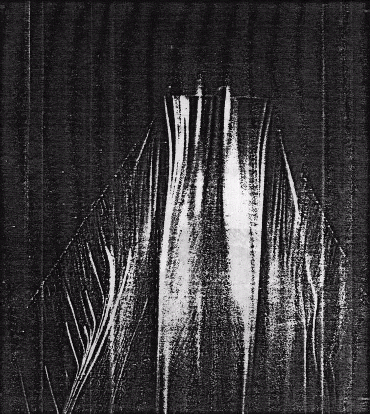
Figure 6. Oil flow photograph of an open separation at M = 1.62
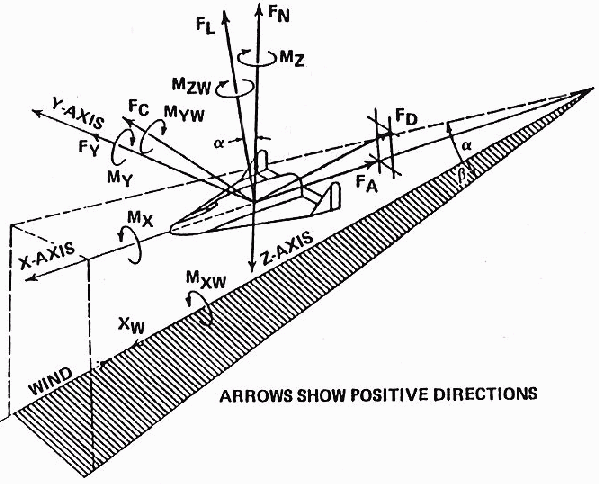
Figure 7. Relation between body and wind axis (Ref. 5)
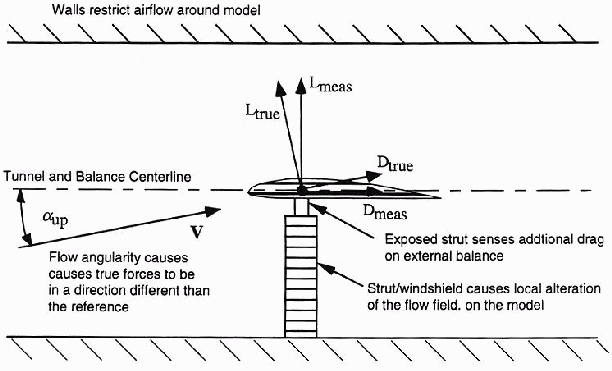
Figure 8. Example of sources of wind tunnel effects requiring data correction.

Figure 9. Boeing scale selection chart (AIAA Student Journal, April, 1971) from Grumman Aero Report No. 393-82-02, April, 1982, "Experimental Pressure Distributions and Aerodynamic Characteristics of a Demonstration Wing for a Wing Concept for Supersonic Maneuvering," by W.H. Mason
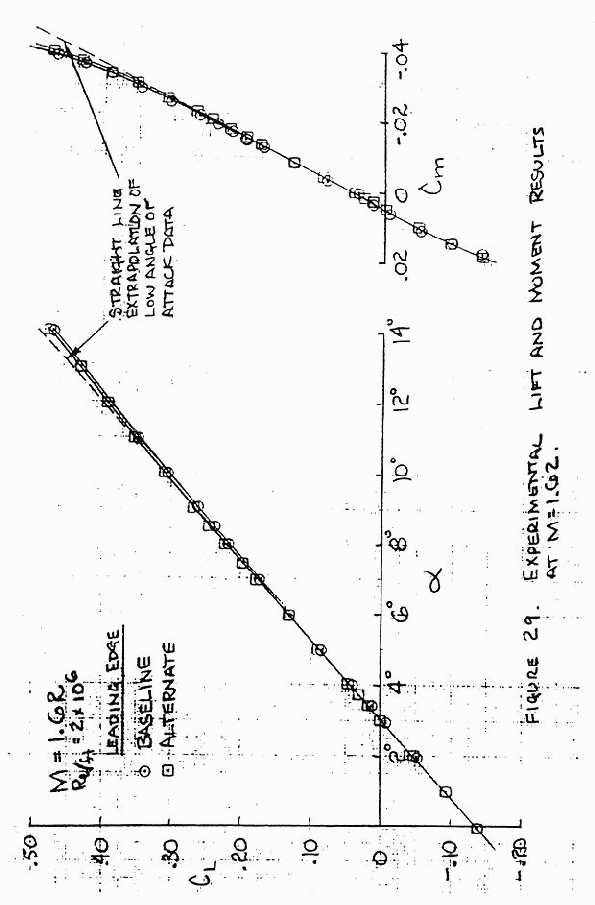
a) lift and moment
Figure 10. Examples of wind tunnel data plots.
from Grumman Aero Report No. 393-82-02, April, 1982, "Experimental Pressure
Distributions and Aerodynamic Characteristics of a Demonstration Wing for
a Wing Concept for Supersonic Maneuvering," by W.H. Mason

Figure 11. Strain gage balance data