Immersed Interface Finite Element Method for Analysis and Design of Multi-Material Systems
Immersed boundary methods are essential to solve multi-material or multi-phase problems, to simulate complex multi-physics processes, and to design optimization with internal and external shapes design variables. Various approaches have been used over the past few decades for immersed boundary FEM including xFEM, GFEM, and Nitsche’s method. The goal of present work is to develop a simple, robust, immersed interface, finite element method for weak discontinuities which can be used for analysis, optimization and uncertainty quantification. The immersed boundary method can be applied to: material distribution and interface sensitivity and design, uncertainty quantification of stochastic multi-material systems and foams, design of material systems with spatially varying physics, e.g., damage, plasticity, chemistry.
The video below shows the deformation and stress on a multi-material system due to applied uniform normal stress at top and bottom edge. The interface between two material (red material is ten times stiffer than blue material) is changed while the underlying mesh remains the same. For these results we prescribed the interface as a function of time. Eventually the interface will be moved over design optimization iterations or will be moved in time due to interface physics like solidification or chemical reaction.
The theory underlying the immersed interface simulation is derived from a non-conformal Petrov-Galerkin formulation. Non-conformal trial functions which satisfy the Hadamard conditions at the interface are used and the test functions are based on standard conformal FEM shape functions. Shown below are the non-conformal trial functions for an example triangular element with an immersed interface.

The immersed finite element method based on non-conformal Petrov-Galerkin formulation (iFEM-ncPG) satisfies the multi-material patch test and thus is guaranteed second order convergence similar to standard FEM method based on interface fitted mesh. Shown below are the exact satisfaction of the multi-material patch test using iFEM-ncPG.
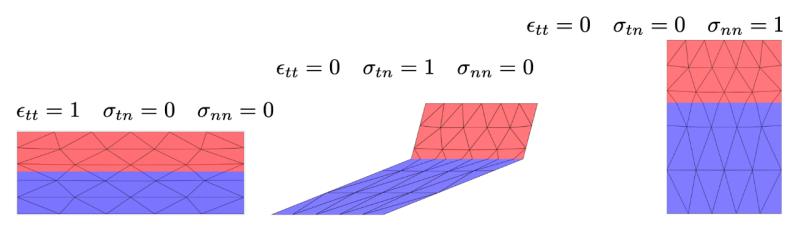
The method is currently being used to design optimal effective materials by varying sub-scale material distribution within a unit cell. Shown below are shear solutions to various square unit cells.
